삼성전자가 세계 물의 날을 맞아 40년 이상 축적해온 폐수 처리 노하우를 공개했다.
삼성전자는 반도체 공정 과정에서 나온 폐수를 3단계에 걸쳐 정화하고, 폐수 처리장에서 한 번 더 처리 과정을 거쳐 하천에 방류한다. 그 과정에 친환경 공법과 자동화를 적용해 작업 안전성을 높였다.
삼성전자는 21일 자사 블로그 ‘삼성 반도체 이야기’를 통해 평택캠퍼스의 폐수 처리 시설인 ‘그린동’을 처음으로 공개했다.
반도체 공정에서 사용된 물은 그린동을 거쳐 고덕 폐수종말처리장으로 이동된다. 그곳에서 처리 과정을 또 거친 다음 평택 진위천으로 방류된다.
그린동은 무기1차 처리, 유기처리, 무기2차 처리 등 3단계로 폐수를 정화한다. 하루 약 7만톤의 물을 정화하는데, 이는 캐리비안베이 담수량의 약 4.7배다.
먼저 무기 처리는 약품의 화학반응을 이용해 불소, 인, 탄소 등 오염 물질을 응집시킨 뒤 찌꺼기를 침전시키는 과정이다. 오염 물질을 방류 기준 이하로 제거하기 위해 1차‧2차로 나눠 진행한다.
특히 알칼리성 폐수를 처리하는 과정에는 친환경 공법을 적용하고 있다. 오염 물질인 과산화수소를 제거하기 위해 과수 제거제라는 화학약품이 아닌 활성탄을 이용하는 것이다.
유기 처리는 미생물을 활용해 질소 등을 제거하는 과정이다. 이 단계는 폐수 처리의 핵심으로, 오염 물질은 미생물이 먹게 하고 기체 상태로 변화시켜 제거한다.
삼성전자는 공정안전관리 기준에 해당하는 고위험 약품인 메탄올을 복합 유기탄소로 대체하는 친환경 공법을 사용하고 있다. 메탄올은 폭발 성질이 있는데 반해 복합 유기탄소는 위험성이 낮다.
탈취 설비에서 악취 성분을 제거하기 위해 일반적으로 사용하는 황산도, 유독성이 없는 인산으로 바꿨다.
이렇게 정화 과정이 끝나면 폐수는 방류관을 거쳐 고덕 폐수종말처리장에서 하천으로 배출된다. 2.6km의 방류구 내에는 산소 농도를 관리하고 기계실처럼 도장해 관리가 용이하고, 안전한 시설을 구축했다.
아울러 삼성은 폐수 처리 업무의 97%를 자동화해서 안전성을 높였다. 약품을 실은 탱크 로리와 약품 탱크를 연결하는 과정을 자동화해서 위험을 없앴고, 설비 내 문제가 생기더라도 중앙통제실(CCR)에서 바로 파악할 수 있다.
약품주입 설비의 배관 이음부마다 플랜지 실드라는 보호막으로 감싸고, 미세 누수까지 초기 감지할 수 있는 감응지 적용해 이중으로 안전장치를 했다. 약품이 이동하는 배관이 있는 곳에는 스크린도어를 설치해 혹시 모를 위험에 대비하고 있다.
삼성전자는 반도체 공정 과정에서 나온 폐수를 3단계에 걸쳐 정화하고, 폐수 처리장에서 한 번 더 처리 과정을 거쳐 하천에 방류한다. 그 과정에 친환경 공법과 자동화를 적용해 작업 안전성을 높였다.
삼성전자는 21일 자사 블로그 ‘삼성 반도체 이야기’를 통해 평택캠퍼스의 폐수 처리 시설인 ‘그린동’을 처음으로 공개했다.
반도체 공정에서 사용된 물은 그린동을 거쳐 고덕 폐수종말처리장으로 이동된다. 그곳에서 처리 과정을 또 거친 다음 평택 진위천으로 방류된다.
먼저 무기 처리는 약품의 화학반응을 이용해 불소, 인, 탄소 등 오염 물질을 응집시킨 뒤 찌꺼기를 침전시키는 과정이다. 오염 물질을 방류 기준 이하로 제거하기 위해 1차‧2차로 나눠 진행한다.
특히 알칼리성 폐수를 처리하는 과정에는 친환경 공법을 적용하고 있다. 오염 물질인 과산화수소를 제거하기 위해 과수 제거제라는 화학약품이 아닌 활성탄을 이용하는 것이다.
유기 처리는 미생물을 활용해 질소 등을 제거하는 과정이다. 이 단계는 폐수 처리의 핵심으로, 오염 물질은 미생물이 먹게 하고 기체 상태로 변화시켜 제거한다.
삼성전자는 공정안전관리 기준에 해당하는 고위험 약품인 메탄올을 복합 유기탄소로 대체하는 친환경 공법을 사용하고 있다. 메탄올은 폭발 성질이 있는데 반해 복합 유기탄소는 위험성이 낮다.
탈취 설비에서 악취 성분을 제거하기 위해 일반적으로 사용하는 황산도, 유독성이 없는 인산으로 바꿨다.
이렇게 정화 과정이 끝나면 폐수는 방류관을 거쳐 고덕 폐수종말처리장에서 하천으로 배출된다. 2.6km의 방류구 내에는 산소 농도를 관리하고 기계실처럼 도장해 관리가 용이하고, 안전한 시설을 구축했다.
아울러 삼성은 폐수 처리 업무의 97%를 자동화해서 안전성을 높였다. 약품을 실은 탱크 로리와 약품 탱크를 연결하는 과정을 자동화해서 위험을 없앴고, 설비 내 문제가 생기더라도 중앙통제실(CCR)에서 바로 파악할 수 있다.
약품주입 설비의 배관 이음부마다 플랜지 실드라는 보호막으로 감싸고, 미세 누수까지 초기 감지할 수 있는 감응지 적용해 이중으로 안전장치를 했다. 약품이 이동하는 배관이 있는 곳에는 스크린도어를 설치해 혹시 모를 위험에 대비하고 있다.
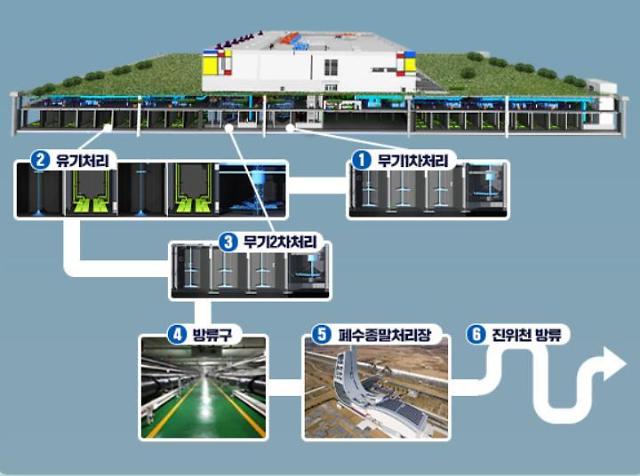
삼성전자 평택캠퍼스 그린동의 폐수처리 과정. [사진=삼성전자 블로그]
©'5개국어 글로벌 경제신문' 아주경제. 무단전재·재배포 금지