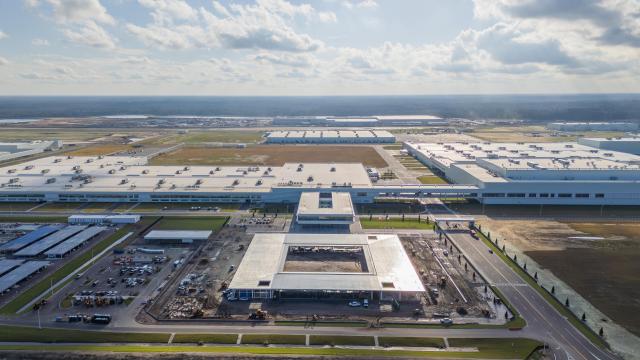
총부지면적 1176만 제곱미터(㎡) 위에 자리잡은 HMGMA는 인공지능(AI), 정보기술(IT), 로보틱스 등 첨단 기술을 융합한 제조 혁신 플랫폼을 바탕으로 현재 현대 아이오닉5, 아이오닉9 등의 차량들을 생산 중이다. 연간 30만대 생산능력을 보유 중이며 향후 기아, 제네시스 차량은 물론 전기차 외에도 하이브리드 모델로까지 생산 라인업을 확대해 나갈 예정이다. 이를 통해 생산능력을 50만대까지 확대한다는 계획이다.
자동차 생산 전 공정에 AI 등 첨단 기술 전방위 접목
HMGMA는 △프레스 △차체 △도장 △의장으로 이뤄지는 자동차 생산 공정 곳곳에 제조 혁신 기술을 적용했다. 패널 홀·크랙 감지 시스템, 도어 간격·단차 자율 보정 장착, 도어 자동 탈부착 등이 대표적이다. 현대차 관계자는 "HMGMA는 효율적인 생산을 실현하는 동시에 작업자의 업무 강도를 낮추는 인간 친화적인 제조 현장으로 탄생했다"고 말했다.
공장에서는 수백대에 달하는 최첨단 로봇 장비들이 높은 생산성과 균일한 품질을 내기 위해 가동된다. 우선 프레스 공장(STAMP SHOP)에서는 6800톤급 초대형 고속(Servo) 프레스(서보 모터에 의해 구동되는 프레스) 5대가 내려찍고 자르는 과정을 반복하며 강판을 차량의 몸이 될 패널로 탈바꿈한다. 차체 패널은 91% 수준의 자동화 공정, 정밀한 성형기술, 고속 이송장치 등을 통해 생산된다. 이후 비전 품질 검사와 AI 기반 품질 관리 시스템을 차례로 거친다. 특히 세계 최초로 적용된 패널 홀·크랙 감지 시스템은 수십대의 카메라를 통해 촬영한 데이터를 딥러닝으로 학습하며 AI 기반 품질 관리를 뒷받침한다.
차체 공장(WELD SHOP)은 로봇들이 일사불란하게 수행하는 용접, 조립 공정을 거쳐 강판 패널들이 자동차의 외관으로 거듭나는 곳이다. HMGMA의 차체 공장은 100% 자동화를 달성했다. 현대차그룹은 도어 간격·단차 자율 보정 장착 시스템을 세계 최초로 자동차 공정 과정에 도입했다. 차체 공정의 마지막 단계인 외관 품질 검사에서는 보스턴다이내믹스의 4족 보행 로봇 '스팟(Spot)'이 가세한다. 스팟이 수행하는 사양 검사와 측정된 품질 정보를 조립 로봇으로 실시간 피드백 보내 고품질 생산을 가능토록 지원하는 간격·단차 검사가 이뤄진다.
도장 공장(PAINT SHOP)은 도료 도포부터 품질 검사까지 높은 수준의 자동화 시스템이 구현됐다. 도포 자동화 시스템은 수작업 대비보다 균일한 도장 품질을 제공하고, 특수 도료 공급 설비는 24개 이상의 다양한 색상을 적용하는 일에 효과적인 대응을 가능토록 한다. 도장 검사 로봇 자동화 시스템은 사람의 눈으로 알아채기 어려운 미세한 문제까지 잡아낼 수 있다.
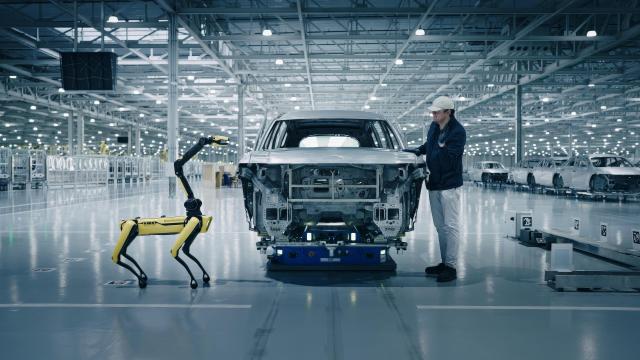
HMGMA 의장 공장에 세계 최초 적용된 도어(차문) 자동 탈거·장착 시스템은 과거 작업자들에게 의존해야 했던 도어 단차 품질 개선과 관리를 자동화한다. 도장 공장에서 넘어온 차체의 도어를 열고, 고정 볼트를 풀어 차량에서 떼어내는 과정 모두를 비전 시스템의 도움을 받은 로봇이 수행한다. 도어를 다시 붙이는 작업에서는 14대의 로봇이 협동 제어를 통해 도어 장착을 마무리한다. 차체와 결합될 각종 자동차 부품은 200여대의 자율이동로봇(AMR)에 실려 각 공정에 적시에 투입된다. AMR은 SLAM 기술을 바탕으로 물류 창고에서 각 공정으로 원하는 위치까지 경로를 생성하며 부품을 배달시킬 수 있다.
이후 완성된 차량은 주차로봇 위에 올라타 자동화된 무인 품질 검사를 거쳐 지정된 최종 목적지까지 이동한 뒤 본격적으로 유통 과정을 개시한다. 주차로봇은 얇고 넓은 형태의 로봇 한 쌍이 차량 하부에 들어가 바퀴를 들어올려 이동시키는 방식으로 구동된다.
HMGMA는 이러한 AI 기반 각종 시스템과 자율로봇 등을 완벽히 통제하고, 공장의 생산 데이터를 디지털화해 운영에 활용하는 소프트웨어(SW) 중심의 공장(Software Defined Factory)으로 구축했다. 이로써 기존 공장에서 작업자들이 무거운 부품을 들거나 윗보기 작업을 반복해야 했던 고전압 배터리, 전후방 섀시 모듈 조립과 같은 공정은 작업자의 신체 부담은 줄이고 부상은 예방하는 인간친화적 형태로 구성했다. 현장 작업자가 고중량의 부품을 들어 반복적으로 볼트를 체결해야 했던 공정은 체결 위치 조정을 포함해 실제 볼트 체결까지 모든 작업이 자동화됐다.
현대모비스·현대제철·현대위아 등 주요 계열사도 '원팀'
HMGMA에는 이와 함께 현대차그룹 주요 계열사의 기술 역량도 모두 망라됐다. HMGMA 부지 안에 있는 현대모비스 배터리시스템 공장·모듈 공장은 현대모비스의 글로벌 생산거점 가운데 최대 규모다. 현대모비스는 이곳에서 SUV를 선호하는 북미 시장의 특성을 반영해 SUV용 대용량 배터리를 포함하는 배터리시스템과 맞춤형 모듈을 생산한다. 현대모비스는 공장 건축 단계부터 전체 라인 설계 과정에 고유의 생산기술 역량을 HMGMA에 집중했다. 또 HMGMA 인근에 전기차 핵심 부품인 PE(Power Electric) 시스템을 생산하는 별도의 거점을 마련해 미국 시장의 전동화 트렌드를 적극 공략 중이다.

현대트랜시스 HMGMA 공장은 연간 42만대 규모의 생산능력을 갖췄으며 아이오닉5, 아이오닉9에 탑재되는 시트를 생산한다. 오토 도킹 시스템, 이형제 도포 로봇(Release agent Spraying robots) 등 최신 자동화 설비를 구축했다. 현대위아는 로봇 기술 역량을 바탕으로 HMGMA의 물류 자동화를 지원한다. 현대위아의 자율주행 운반 로봇(AGV)은 생산에 필요한 각종 자동차 부품을 입고하고 보관하는 등 생산계획에 맞춰 각 공정에 적시 공급한다. 주차로봇은 완성된 자동차를 무인 품질 검사 등의 공정으로 안전하게 운반한다. 현대로템은 차량 강판을 차체 패널로 만들어주는 서보 프레스 설비를 HMGMA 현장에 공급하며, 고품질의 자동차가 생산될 수 있게 지원했다. 각종 차량 부품을 생산 공정으로 옮기는 공장 운반 설비도 담당했다.
향후에는 현대차그룹 로봇 전문 계열사 보스턴다이내믹스의 휴머노이드 로봇 '올 뉴 아틀라스(All new Atlas)'가 시범 투입될 예정이다. 최근 보스턴다이내믹스는 생산 현장 투입을 앞두고 아틀라스의 AI 학습을 강화하고 있다. 추후 아틀라스가 부품 운반 등 단순 반복 작업에 투입될 경우 작업자의 부담을 덜어주며 생산성, 효율성 향상에 기여할 것으로 기대된다.
©'5개국어 글로벌 경제신문' 아주경제. 무단전재·재배포 금지